Structural and Vibration Analysis of Bracket Design
Challenges:
- Developing geometric model of the bracket having higher natural frequencies than the engine
- Developing finite element model to perform structural and modal analysis
- Apply specific material and load data to ensure result accuracy
- Evaluate the bracket model for worst loading conditions
Output:
- Negative Angle is the absolute angle between the box inclination with absolute.
- For all the loading conditions, Maximum Equivalent Stress is less than the permissible (540MPa for Carbon Steels)
- For all the loading conditions, Maximum Shear Stress is less than permissible(270 MPa for Carbon Steels)
Software Used: ANSYS Professional NLS 14.5
Solution: Hi-Tech’s FEA analysts developed bracket model with higher natural frequency than the engine, and optimized the design for worst case loading conditions through static structural and modal analysis.
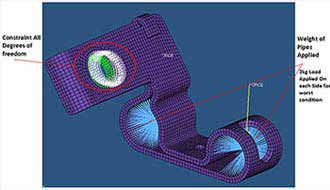

Brackets play a vital role in supporting hoses in automobile applications. Components requiring high pressure fluid for their operation make use of hoses and pipes connected with high complexity. These hoses need support from brackets in order to maintain their position rigidly and avoid any movement. As a result, brackets are required to possess the necessary strength to hold the hoses as well as prevent any vibration due to the engine operation.
One of the leading aftermarket manufacturers of fluid conveying products approached Hi-Tech with a similar problem. The customer was in need of developing an optimized bracket design to adequately support the hose pipes rigidly, without exciting under the engine vibration.
Solution
In order to address the problem, an initial design provided by the customer was re-modeled with optimized geometrical dimensions, to ensure that the bracket’s natural frequency was well above the engine’s operating frequency, avoiding the possibility of resonance.
The revised model was utilized to perform static structural and modal analysis using finite element method. It was found that the new proposed bracket design was well within the allowable stress limits and nominal deformation. To evaluate the structural strength of the bracket in worst conditions, the load due to pipe was doubled and the results were found within the permissible range. Through modal analysis, the natural frequency of the bracket was measured well above the operating frequency of the engine.
Benefits
- Optimized bracket design with the ability to withstand 2Kg of pipe load
- Detection of regions of higher stress concentration in the design
- Improvement in design quality and 70 % reduction in product development cycle
- Reduction in unnecessary vibrations which may lead to pipe damage and failure